RTR Boiler Economizer Series
Rectangular Tube Recovery
The RTR (Rectangular Tube Recovery) boiler economizer is ideal for large steam boilers and hot water boilers. The RTR is typically used to preheat boiler feedwater, process water, hot oil, or cold water condensing applications. A variety of heat transfer surfaces are available, including: 316L stainless steel, carbon steel, duplex stainless steel, and stainless steel tube with aluminum bonded AL-FUSE™ product. The exclusive, standard feature, internal stainless steel exhaust gas bypass can be used to temper the exiting gas for stack corrosion control or to maintain water temperatures when too much heat is available.
Combustion Sources
Steam boilers, hot water boilers, and hot oil heaters with inputs up to 250,000,000 BTU/hr.
Boiler Exhaust Application
Capacity: up to 250,000 lb/hr steam
Entering Gas Temps: 300°F to 800°F
Heat Sink Types: boiler feedwater, makeup water, hot water return, hot water storage tank, condensate tank, process water
Variety
One feature of the RTR product line is the large variety of sizes and configurations that are available. Cain Industries routinely produces RTR models that range in application size from small 50 hp boilers to massive 250,000 pph boilers. In addition, RTR units can be engineered to function in a horizontal or vertical stack and can be outfitted with optional automatic sootblowers.
- Constructed with a 10 gauge structural exterior, a stainless steel interior designed for expansion and 2" of factory insulation.
- Single row finned tubing design (maximum of 2 rows in the path of the exhaust flow) allows full access to the entire heating surface and provides ease of cleaning and maintenance. Most models have no pressure welds in the gas stream.
- Exterior liquid manifolds maintain very low liquid pressure drop, eliminating the need for extra pumps/HP. The manifold is connected to the finned tubes with compression fittings which allow a finned tube to be removed for inspection or replacement without requiring any welding.
- Exclusive Cain compression fittings between finned tubes and the liquid manifolds for easy tube removal that requires no welding.
- Mounting flanges and adapters are integral to Cain Industries economizers, reducing installation time and providing a superior connection between the existing stack and the Cain unit.
- Exhaust stack adapters allow the RTR to provide maximum heat recovery while mating perfectly with an existing exhaust stack. Adapters also allow the rectangular RTR to work with a round exhaust stack.
- Removable access doors provide a complete view of the finned tube heating surface for inspection, repair, or maintenance. This reduces downtime and labor expenses.
- Internal stainless steel bypass diverter allows the amount of exhaust gas diverted through the economizer to be modulated to achieve desired heat recovery. This becomes an important safety feature when you recover more heat than required by the existing system.
- Equipped with a condensate drain catch ring assembly.
- Modulating bypass actuator assembly for automatic operation
- Hinged inspection doors for immediate access
- Timed automatic sootblower assembly provides blowdown without scheduling personnel
- Stack corrosion control assembly
- Liquid temperature control assembly
- Structural support stand
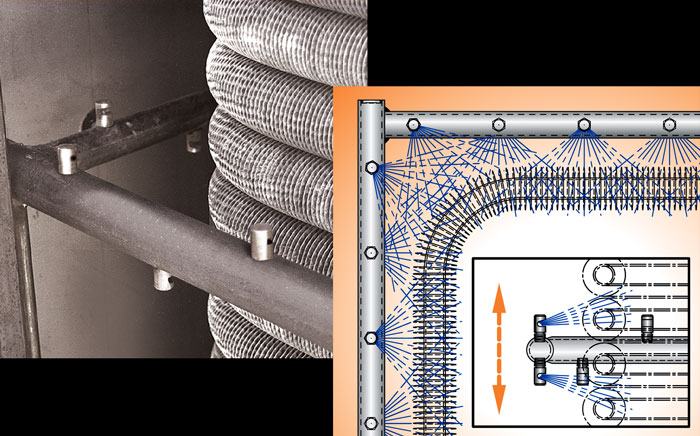
Timed Automatic Sootblower (optional)
The exclusive Cain Industries Timed Automatic Sootblower design is applied where sulfur content is high or combustion is poor. The special flood-jet type nozzles achieve maximum cleaning velocity using steam or air discharged through an electric control valve. Together they form a “continuous knife edge concentrated spray pattern” surrounding the heating surface. This “ring nozzle assembly” is attached to a manifolded flexible steel hose assembly and is powered back and forth by a pneumatic drive cylinder. Dual timing relays allow full control of cycle duration and interval. Cleaning the finned tubing ensures maximum BTU recovery and maximum cost savings. Fouled finned tubing can reduce heat recovery by up to 50%.
Proper sootblowing is necessary when fuel has a high sulfur content or combustion is poor (such as No. 6 fuel oil). Without sootblowing, the finned tubing will become fouled and the maximum heat recovery cannot be achieved.
The traveling Ring Assembly with Flood-Jet Nozzles, form a unique high velocity knifing action to allow full penetration of the complete heating surface. The Cain Industries sootblowing system is unsurpassed in the marketplace for effectiveness and efficiency.
Built-in timing relays allow you to customize the interval and duration to suit your application.